Introduction
If you’ve lived in Florida for any length of time during the summer, you’ve either told someone to “close the door…you’re letting the cool air out” or you’ve been at the receiving end of the same message. Any openings in the shell or envelope of your home, whether big (like an open door) or small (like around an electrical socket on an outside wall), can allow conditioned air (i.e., cooled or heated) to “leak” out, or let unconditioned air into your home. Uncontrolled inward air leakage is referred to as “infiltration”.
For infiltration to occur there has to be a source, a hole, and a driving force (like the wind or an interface between high and low temperature or humidity, etc.). So if you air condition a building, which also helps reduce indoor humidity, the high-humidity outdoor air can still enter your home through large openings like open doors and windows and small openings like cracks and crevices in the building shell, thereby leading to possible air quality problems. In Florida, the first noticeable signs of an air leakage or infiltration problem are when our homes become either uncomfortable (hot and/or damp) and/or our energy bills are extremely high (typically in summer months).
How do air leaks occur?
Building contractors install certain features to intentionally ventilate and exhaust unwanted odors or combustion byproducts from your home—such as exhaust fans in your bathroom and above the stove. Unintentional air leakage is undesirable, however, and can occur because of the construction techniques used and/or lack of attention to proper air sealing during construction. As homes age and settle, air sealants may fail, which can also contribute to unintentional air leakage. Even remodelers or repair professionals can unintentionally cause or exacerbate air leakage problems in your home. Think of the remodeler changing out your kitchen cabinets and leaving an opening to the attic above the cabinets, or the cable technician drilling a hole in the side of your home to place a cable line and failing to seal the hole properly after the cable is installed. Building contractors, who have blower door tests performed on homes they build, learn to expect where and how air leakage problems are likely to occur, and they have adopted construction techniques to avoid such problems.
How can we measure air leakage in buildings?
It would of course be almost impossible to identify and measure all of the cracks and holes present in any given building’s shell. Yet these leak sites can be measured indirectly with a “blower door test.” The blower door test measures the airtightness of a building by changing the building’s static pressure with respect to the outdoors and recording the amount of air flow required for that change. The greater the air flow required to change this static pressure relationship, the greater the total size of the cracks and holes in the building envelope.
Results of the blower door test provide a standard measure of the leakage of a home, measured in cubic feet per minute (CFM) of airflow. This number is then converted to air changes per hour so you can compare your home’s leakage to standard recommendations for healthy and energy-efficient homes. While less leakage is typically considered better, keep in mind that a home that is “too tight” (i.e., very little leakage) can also cause poor indoor air quality, which in turn can contribute to health problems for building occupants
When and why should you have the blower door test done to your home?
The blower door test is often required to determine if a home meets part of the criteria for energy efficiency or “green status” of many building certification programs. These third-party certification programs generally offer monetary incentives for building owners and/or the licensed building contractor of homes that meet or exceed program requirements. For example, the Weatherization Assistance Program (WAP) requires a blower door test to assess where air leakage is occurring before approving any upgrades to the home. Some utility companies offer incentives or rewards to builders and/or homeowners who test homes with the blower door test and install measures to reduce air leakage. (Keep in mind that the standard blower door test does not involve identifying where leaks occur, only quantifying the amount of leakage.)
A home buyer’s/owner’s incentive for having a blower door test done, in addition to reduce utility bills, may include mortgage inducements. If a home is reasonably air tight, the heating and cooling systems do not have to work as hard to maintain a comfortable indoor air temperature, and the utility bill will generally be lower than it would be if the home were “leaky”. If you’re thinking about purchasing a home, whether new or pre-owned, you may want to consider having a home energy rating done before you buy. The home energy rating will include a blower door test to identify building leakage problems. There has been a voluntary statewide energy-efficiency rating system for Florida homes since 1994 and unplanned air leakage is a major factor determining the overall home energy rating. More information about home energy ratings can be found in this fact sheet.
While there are many well-known sources of air leakage – the “usual suspects” – almost all buildings have unexpected air leakage sites called bypasses. These sources of leakage can be difficult to locate and correct without the use of the blower door test. See this guidebook, Thermal Enclosure System Rater Checklist, for information on thermal bypasses and this publication, Retrofit Techniques & Technologies: Air Sealing, for more information on air sealing.
Why the funny name – “blower door” – to the test?
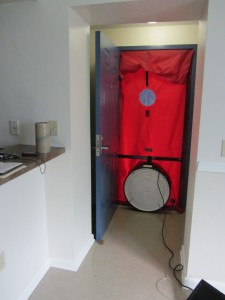
Figure 1. A blower door test set-up on a home as it appears from the inside of the building. Credit: PREC
There are a number of steps involved with a blower door test. First, a temporary frame is placed in an exterior door frame. This frame is generally covered with a piece of vinyl or canvas specifically made for blower door testing. Second, a fan (i.e., “blower”) is placed in the opening at the bottom of the temporary frame. Hence, the “blower door” test. As part of the test, the fan can either pressurize (force air into the house) or depressurize (force/pull air out of the house). Figure 1 shows how the setup appears from outside the home.
In addition, the blower door test uses a pressure gauge (manometer) that measures the fan pressure relative to the location from which air is entering the fan (Figure 2). This pressure is converted to air flow measurements as the air passes through the fan.
Who can do the test?

Figure 2. A view from the inside of the home showing the blower door test equipment: a temporary door (frame), blower (fan), and manometer (pressure gauge) along with helpful tools including a laptop computer, clipboard and blueprints of the home. Credit: PREC
Generally, for “green” certifications requiring a blower door test, a RESNET Home Energy Rating System (HERS) Rater must conduct the test. ENERGY STAR Home program testing can only be conducted by RESNET HERS Raters who have taken and passed an ENERGY STAR certification class. To find a RESNET HERS Rater who can conduct a blower door test for “green certification” purposes, search this website.
For 5th Edition (2014) Florida Energy Conservation Code residential air leakage testing, per Section R402.4.1.2 of the code, where required by the code official, air leakage testing must be conducted by an approved third party. Per Chapter 2 of the same code, an approved third party means one who is approved by the code official. Requirements for air leakage testing in the Florida Building Code have been delayed for up to a year from the date of this publication (June 22, 2015). Consult your local Building Department for the status of the building air leakage testing requirements.
Some Florida utilities offer incentive programs that do not require a RESNET HERS Rater but instead have energy conservation services staff that are qualified to conduct the test while also providing an energy audit.
How is the test conducted?
In Florida, it is very common during a blower door test to operate the fan in the depressurizing mode, meaning that air is drawn, pulled or exhausted out of the house. When the fan operates in this way, it is easy for someone walking around inside the home to feel air entering the building through cracks in its exterior envelope (shell). This infiltration commonly occurs around windows, recessed lights, electrical sockets, air handlers, or any feature that penetrates the exterior walls or roof. Inside air leaving the home through the blower (exhausting) has to be replaced with outside air entering the building elsewhere—what goes out, must come in—so spots where air can be felt entering the building are air leakage sites/sources.
There are a number of websites that show blower door tests being performed. See for example this video.
What do the numbers from the test mean?
One measure of a building’s air leakage rate is air changes per hour (ACH), which estimates how many times in one hour the entire volume of air inside the building is exchanged with outside air. To determine a building’s ACH, the blower door performs an airtightness test with the house depressurized (or pressurized) to 50 Pascals. A Pascal (Pa) is a small unit of pressure about equal to the pressure that a pat of butter exerts on a piece of toast. Fifty Pascals is approximately equivalent to a 20 mile-per-hour wind blowing against all surface of the building.
The leakier the house, the higher the number of air changes per hour, the higher the heating and cooling costs, and the greater the potential for moisture, comfort, and health problems. Builders of energy-efficient homes generally strive for less than 5 air changes per hour at 50 Pascals pressure (ACH50). Table 1 summarizes the ranges of air changes per hour for typical homes of different levels of air leakage and energy efficiency.
Table 1. Typical infiltration rates for home ACH50 (Air changes/hour at 50 Pascals)
New home with special airtight construction and a controlled ventilation system | 1.5 – 3.0 |
Energy-efficient home with continuous air barrier system (based on registered ratings) | 3.0 – 5.0 |
Standard new home (based on registered ratings) | 5.0 – 7.0 |
Standard existing home (based on field data) | 7.0 – 10.0 |
Older, leaky home (based on field data) | 10.0 – 5.0 |
To determine the ACH50, we first determine the amount of air flow, measured in cubic feet per minute (CFM), exhausted out of the home with the home at a pressure of 50 Pa with respect to the outside. To calculate this, air flow readings are taken at several house pressure differences, generally between 15 and 60 Pa. These measurements are then entered in a software program to determine the air flow rate at 50 Pa (referred to as CFM50). Multiplying the resulting CFM50 value by 60 (minutes) and dividing by the conditioned volume of the house (in cubic feet) gives the ACH50. For example, a home that has 2,000 square feet of living area and 8-foot ceilings has a volume of 16,000 cubic feet (2,000 square feet multiplied times 8 feet). If the blower door measures a CFM50 leakage of 1,333 then the equation would be 1,333 cubic feet per minute times 60 minutes divided by the volume of 16,000 cubic feet to equal 5 air changes per hour. The home therefore has an infiltration rate of 5 ACH50 (5 air changes per hour at 50 Pa test pressure).
Given ACH50, a natural infiltration rate (resulting from wind and temperature effects) can be estimated for your home. In Florida’s climate, ACH50 measures can be divided by 40 to yield an expected natural infiltration rate, measured as “ACH” (Cummings, Moyer, and Tooley, 1990). For example, if ACH50 = 10 for a Florida home, then the estimate for its natural infiltration rate would be 10/40, or 0.25 ach. This means that under normal wind and temperature conditions, we would expect about 25% of the house air to be replaced with outdoor air each hour with no mechanical equipment running. Note that this is only an estimate of long-term average infiltration. Actual infiltration will vary considerably based on time of day and changes in wind, temperature, and humidity over the course of the day.
In the example home above, with an ACH50 of 5, the expected natural infiltration rate would be 5 divided by 40, or 0.12 ach. This means that under normal wind and temperature conditions, we would expect about 12% of the house air to be replaced with outdoor air each hour.4
How big are the air leakage sites (“holes”) in my house?
Now that you know the CFM50, which is the air flow through the building’s leak sites at a 50 Pa house pressure differential, we can determine the approximate cumulative size of the holes. The “holes” in this case are areas of air leakage. In other words, you are trying to determine the approximate size of all the air leakage sites added together. To do so, multiply the CFM50 by 0.13. In our example above, where CFM50 was 1,333, what the approximate cumulative hole size would be 1,333 times 0.13, or 173 square inches. This means that if you added all the air leak sites together in the example home you would find 173 square inches (1.18 square feet) of potential areas that need sealing, caulking, fixing, or some other sort of repair to reduce leakage.
Are there any limitations to the blower door test “finding” leaks?
As helpful as the blower door test is in measuring and helping to identify areas of air leakage, it’s important to understand that the blower door test does have limitations with respect to locating all sources of leaks. For instance, sometimes indirect leaks or a combination of very small leaks can exist that cannot be easily identified with a blower door test. In such situations, other tools such as infrared thermometers or cameras (discussed later in this fact sheet) can be used to detect changes in temperature that are indicative of air leakage.
What about testing the duct system for leaks?
There are a number of tests that can be performed to determine if duct systems in a home are working efficiently. If ducts are not installed correctly, the mechanical systems can be leaky and/or using more energy than necessary. For example, if ducts are located outside the conditioned area of the home, such as in the attic, and they are leaking, the homeowner may not realize they are paying to heat or cool the air outside their living environment.
Auditors and energy raters often use a tool referred to as a duct airtightness tester that can depressurize or pressurize the duct systems and determine the amount of air leakage (Figure 3). The use of a pressure pan in conjunction with the blower door can isolate where ducts are “leaky”. The pressure pan resembles a large cake pan. This test and/or a “smoke” test can be used to help locate duct leaks once a duct airtightness test determines that sealing would be warranted.
What are some other tests that might be performed along with a blower door test?
Remember the example given at the beginning of this fact sheet about letting hot air enter an air-conditioned home? Anything that emits heat also gives off infrared radiation—the greater the heat, the more infrared radiation. Infrared thermometers and cameras can be used to detect air leakage sites as air leakage heats or cools surfaces. When used with a blower door, the leaks are much more noticeable. Although primarily written for North Dakota conditions, the publication Determining Insulation and Air Infiltration Levels Using an Infrared Thermometer provides useful information on the process of evaluating your home for air leaks using an infrared thermometer. There are a wide variety of infrared cameras, but with all models it is critical that the user know how to correctly operate the camera and interpret the visual images.
Added Value of the Florida Energy Systems Consortium
Methods to make homes more energy efficient yet still provide adequate ventilation may originate or be refined from research currently being conducted by faculty affiliated with the Florida Energy Systems Consortium (FESC). From technical research to policy evaluation to behavioral campaigns and community outreach, FESC is helping Floridians reduce energy consumption and demand while creating a healthier environment.
Additional References and Resources
Cummings, J.B., Moyer, N., and Tooley, J.J. November 1990. Radon Pressure Differential Project, Phase II: Infiltration. Florida Solar Energy Center, Cocoa, FL. FSEC-CR-370-90.
Blower Door and Duct Leakage Testing for Duct & Envelope Tightness Verification. (PDF 50 KB). (March 2011). Energy Fact Sheet 22. Atlanta, GA: Southface Energy Institute.
5th Edition (2014) Draft. Florida Building Code: Energy Conservation. Chapter 4: Residential Energy Efficiency.
Van der Meer, B. Blower Door Testing. Builder Brief BB0201. The Pennsylvania Housing Research/Resource Center. Boulder CO.
Acknowledgements
Authors: Craig Millera and Tei Kucharskib
Reviewers: Neil Moyerb, Jeff Sonneb, and Jennison Searcya
First published July 2010. Updated April 2015.
a Program for Resource Efficient Communities, Florida Cooperative Extension Service, Institute of Food and Agricultural Sciences, University of Florida, Gainesville, FL
b University of Central Florida, Florida Solar Energy Center, Cocoa, FL,
This is a fact sheet produced for the Florida Energy Systems Consortium (FESC). The goal of the consortium is to become a world leader in energy research, education, technology, and energy systems analysis.